Technical Focus
LC-FINING UNIT
One of the key units to be built as part of the BMP is a Resid Hydrocracking Unit (1RHCU) which is powered by technology licensed from Chevron Lummus Global (CLG). The BMP team is building a two train RHCU with a capacity of 65,000 bpd.
Less than a dozen of these units exists globally, and Bapco’s 1RHCU will be among the largest on the planet. The plot size for 1RHCU is approximately 260m x 260m — equivalent to 10 football pitches.
The RHCU converts 78 per cent of the vacuum residue feed into intermediate products (distillates) which will then be further processed into high margin naphtha, kerosene, and diesel.
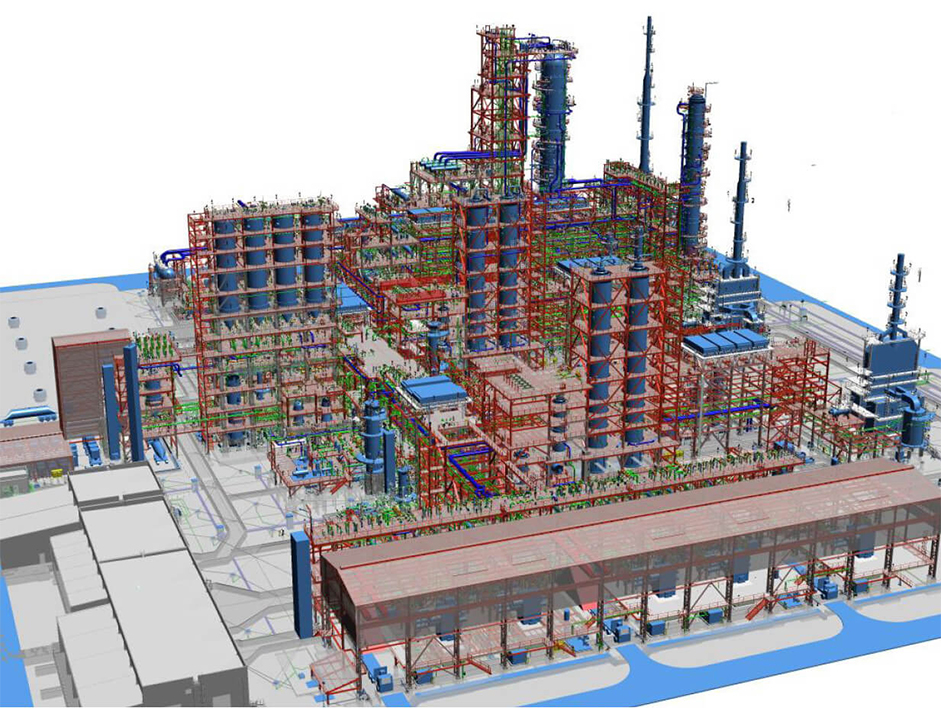
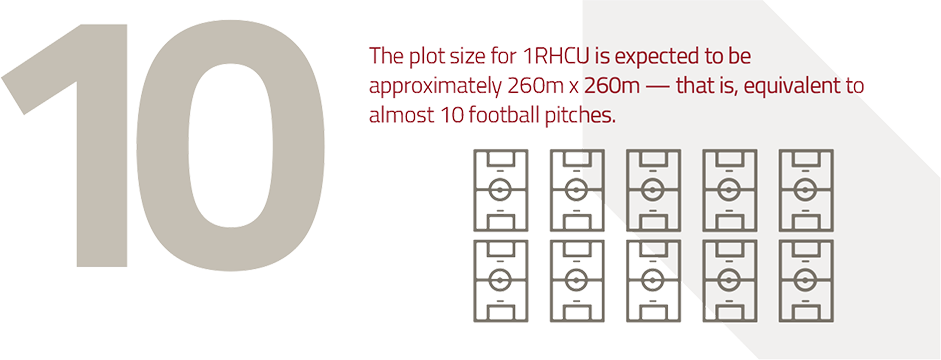
NEW CRUDE AND VACCUM DISTILLATION UNITS
The BMP also includes the new Crude and Vacuum Distillation Units. This new state-of-the-art 225,000 bpd integrated crude and vacuum unit will replace five existing distillation units, which have served Bapco for over 80 years. The new units will provide the required feedstock for further downstream processing, increasing the refinery capacity up to 400,000 bpd.
Using advanced heat recovery installations, the units maximize output with minimum amount of energy consumption, and thus fulfilling a key BMP objective. The units increase crude output by +42 per cent of the previous refining capacity.
Key features of 7CDU include desalters and a two-drum overhead system which removes corrosive elements from the raw crude and enhances the reliability of the unit and allows processing of a heavier feedstock as needed. The 7CDU heater is energy efficient and has a duty of 445 MM Btu/hour and 36 low NOx burners. An additional key feature of 7VDU is the deep vacuum mode that helps the unit in maximising product yields. These distillation units physically separate crude oil into valuable petroleum distillates like LPG, Naphtha, Kerosene and Diesel, and also in preparing the remaining heavy oil fraction for further processing in the secondary conversion units (VGO Hydrocracking and LC-FINING hydrocracking).
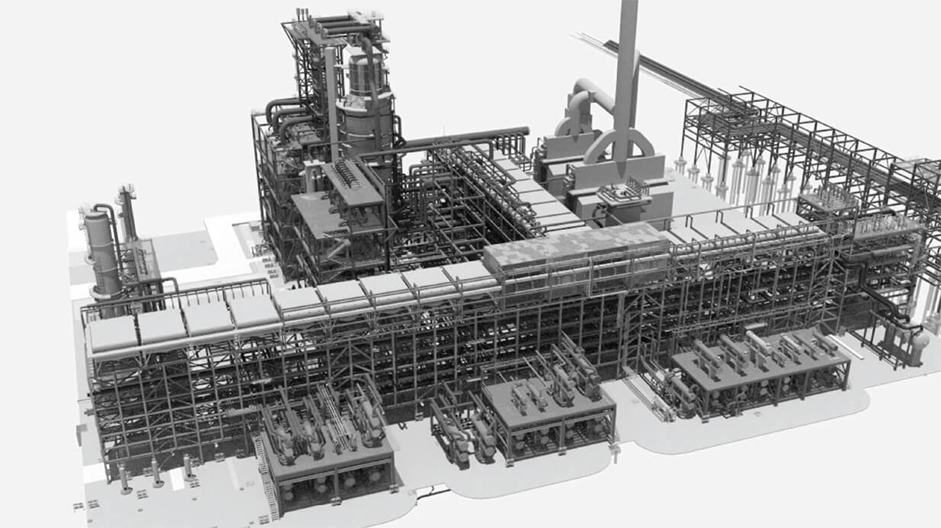
SECOND VGO HYDROCRACKER
No. 2 VGO Hydrocracking Unit is one of the most important conversion units in the refinery. Its configuration is similar to the existing No.1 Hydrocracking Unit. The new unit has a higher capacity and greater complexity, in particular regarding its advanced waste heat recovery scheme, maximizing energy efficiency.
The unit is a single train with two stages of reaction, having a capacity of 58,000 barrels of Vacuum Gasoil per day, converting 99% of the low value feed into higher margin final products, namely middle distillates (Kerosene and Diesel). It has both the heaviest and tallest columns in the Refinery.
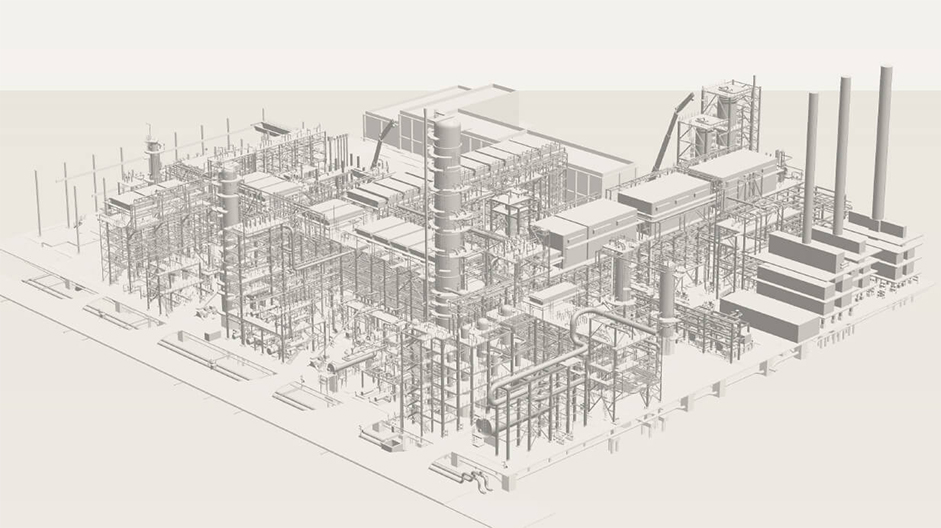
NEW SULPHUR PLANT
The #3 Sulphur Plant is a sulphur recovery, amine and sour water treating facility built as part of the BMP, and comprises of eleven process units, at half a kilometre length is one of the longest blocks at the BMP site.
The plant’s main purpose is to recover H2S from the BMP Units’ process streams and convert it into liquid sulphur. The liquid sulphur is then converted into solid pellets in a separate unit, with the final product exported abroad.
This plant includes several units, including Sulphur Recovery Units, Tail Gas Treating Units, Bulk Acid Gas Removal Units, Amine Regeneration Units, and Sour Water Stripping Units. The new Sulphur Recovery Units add 750 Tonnes/Day capacity, leading to a refinery total sulphur production capacity of 1,535 MT/Day.
Technology and unit configuration is similar to the existing SRUs including a two-stage Claus Process followed by tail gas treatment, giving 99.9% recovery of H2S. However, there are two notable differences, including air sweep degassing, heat recovery, and steam generation systems.
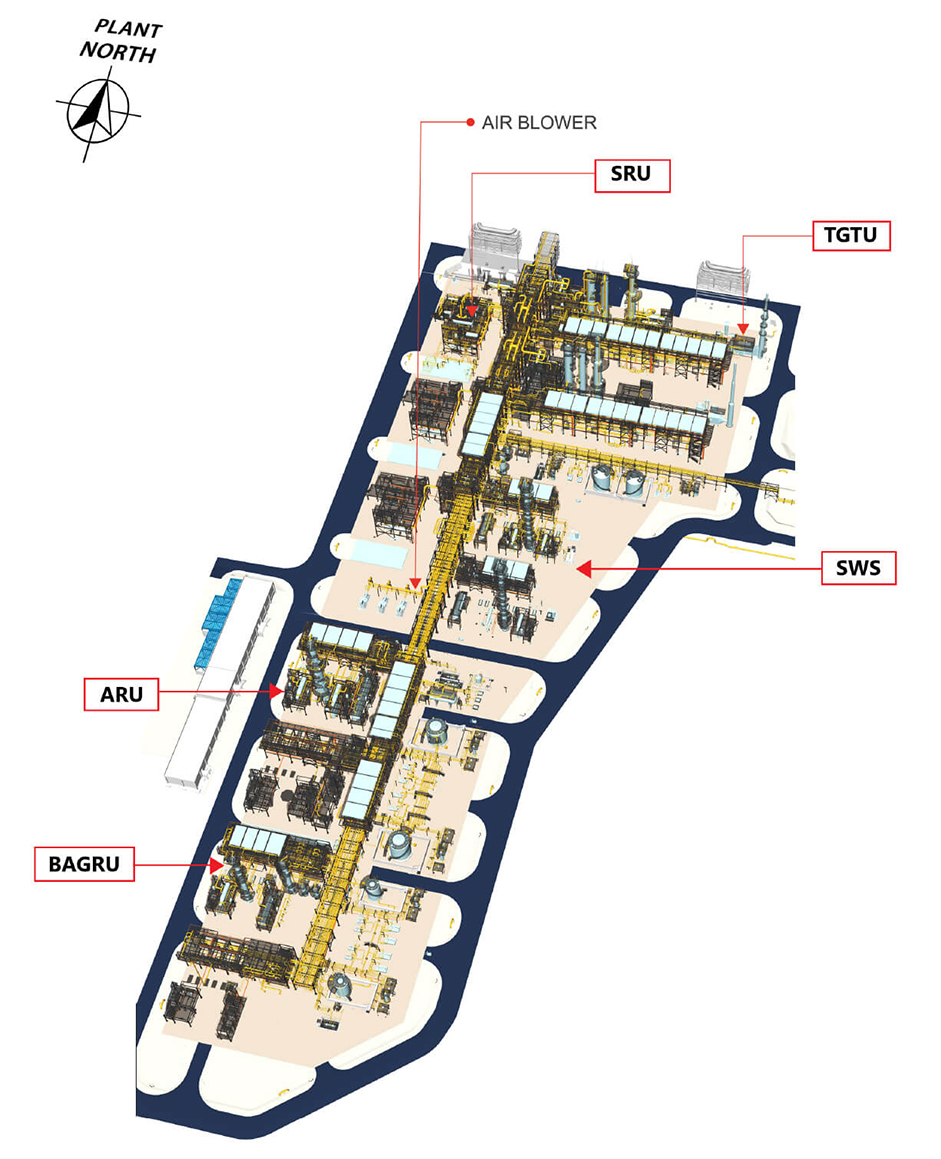